en产品中心
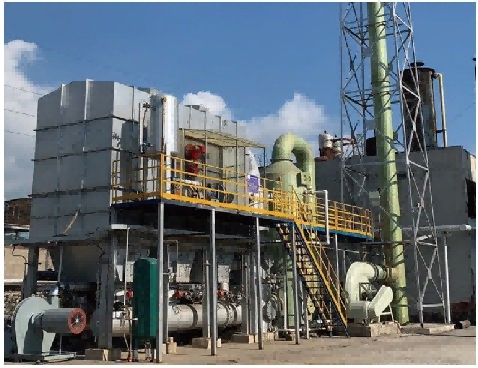
Regenerative thermal oxidizer
Product Overview
Principle introduction: The exhaust gas is sucked by a fan into the heat storage chamber, where it exchanges heat with the heat storage ceramic. The exhaust gas is preheated to around 750 ℃ and then enters the thermal oxidation chamber for full oxidation and decomposition. Under the action of combustion supporting fuel, the temperature of the thermal oxidation chamber reaches over 800 ℃, and the organic components in the exhaust gas are completely oxidized and decomposed. The flue gas generated in the thermal oxidation chamber enters the heat release chamber for heat release, and the temperature drops to around 70 ℃. The flue gas then enters the spray washing tower for spray washing, Finally, the smoke is discharged into the atmosphere through the chimney. When the organic content in the exhaust gas is high, some of the flue gas enters the waste heat recovery equipment to recover the waste heat of the flue gas. This thermal oxidation device is equipped with multiple heat storage chambers, each arranged in a straight line shape, which can automatically and periodically switch the working status of the heat storage chambers.
Furnace type classification:
☆ Multi box RTO device
☆ Rotating RTO device
☆ Wheel concentration+RTO device
☆ New Water Seal Explosion Relief Device
☆ Combined exhaust gas pretreatment device
Heat recovery method:
☆ Heat transfer oil heating
☆ Saturated steam
☆ Hot air or hot water
☆ Combined flue gas pretreatment device
Processing scale and scope of application:
☆ Processing capacity: 0.2-100 × 104m ³/ H
☆ Treatment method: thermal storage oxidation
☆ Scope of application: rubber, textile, pharmaceutical, chemical synthesis coating drying room, shoe coating printing color printing, petrochemical, phthalic anhydride (PA), maleic anhydride (MA), PTA exhaust gas
Structural characteristics:
☆ Adopting a regenerative heat exchange device, the heat storage carrier directly exchanges heat with the gas, resulting in high furnace radiation temperature and pressure, fast heating speed, significant low-temperature heat exchange, significant energy-saving effect, reduced fuel consumption, and reduced greenhouse gas emissions.
☆ The temperature in the heat storage room is evenly graded to increase, strengthening the heat transfer inside the furnace and achieving better heat exchange effect.
☆ Due to the fact that the flame gradually burns in the high-temperature storage body inside the furnace, without a high-temperature front, the combustion noise is low.
☆ Expanded the high-temperature flame combustion area, resulting in uniform furnace temperature, improved purification efficiency, and extended furnace life.
☆ Adopting graded combustion technology, it releases heat energy under delayed combustion and has good heating effect. It inhibits the generation of thermal nitrogen oxides and has good environmental protection effects.
☆The overall temperature in the combustion chamber increases and the distribution becomes more uniform. The furnace temperature can reach 850-1100 ℃, with high airflow speed, fast combustion speed, long flue gas residence time, and complete decomposition of organic oxides.
☆Adopting PLC automatic combustion control, with high degree of automation, stable operation, and high safety and reliability.
☆According to the situation of waste gas, a heat recovery device can be reasonably set up, and the high-temperature combustion chamber can be connected to a thermal oil furnace or a waste heat boiler. The low-temperature flue gas is used to heat the waste gas and fully utilize the waste heat.
☆The thermal storage incinerator can adopt a flue gas reverse blowing structure based on the composition of the exhaust gas.
☆While incinerating exhaust gas, wastewater or waste liquid can be incinerated. Wastewater and waste liquid can be incinerated using our company's proprietary technology: a combined combustion unit.
Furnace type classification:
☆ Multi box RTO device
☆ Rotating RTO device
☆ Wheel concentration+RTO device
☆ New Water Seal Explosion Relief Device
☆ Combined exhaust gas pretreatment device
Heat recovery method:
☆ Heat transfer oil heating
☆ Saturated steam
☆ Hot air or hot water
☆ Combined flue gas pretreatment device
Processing scale and scope of application:
☆ Processing capacity: 0.2-100 × 104m ³/ H
☆ Treatment method: thermal storage oxidation
☆ Scope of application: rubber, textile, pharmaceutical, chemical synthesis coating drying room, shoe coating printing color printing, petrochemical, phthalic anhydride (PA), maleic anhydride (MA), PTA exhaust gas
Structural characteristics:
☆ Adopting a regenerative heat exchange device, the heat storage carrier directly exchanges heat with the gas, resulting in high furnace radiation temperature and pressure, fast heating speed, significant low-temperature heat exchange, significant energy-saving effect, reduced fuel consumption, and reduced greenhouse gas emissions.
☆ The temperature in the heat storage room is evenly graded to increase, strengthening the heat transfer inside the furnace and achieving better heat exchange effect.
☆ Due to the fact that the flame gradually burns in the high-temperature storage body inside the furnace, without a high-temperature front, the combustion noise is low.
☆ Expanded the high-temperature flame combustion area, resulting in uniform furnace temperature, improved purification efficiency, and extended furnace life.
☆ Adopting graded combustion technology, it releases heat energy under delayed combustion and has good heating effect. It inhibits the generation of thermal nitrogen oxides and has good environmental protection effects.
☆The overall temperature in the combustion chamber increases and the distribution becomes more uniform. The furnace temperature can reach 850-1100 ℃, with high airflow speed, fast combustion speed, long flue gas residence time, and complete decomposition of organic oxides.
☆Adopting PLC automatic combustion control, with high degree of automation, stable operation, and high safety and reliability.
☆According to the situation of waste gas, a heat recovery device can be reasonably set up, and the high-temperature combustion chamber can be connected to a thermal oil furnace or a waste heat boiler. The low-temperature flue gas is used to heat the waste gas and fully utilize the waste heat.
☆The thermal storage incinerator can adopt a flue gas reverse blowing structure based on the composition of the exhaust gas.
☆While incinerating exhaust gas, wastewater or waste liquid can be incinerated. Wastewater and waste liquid can be incinerated using our company's proprietary technology: a combined combustion unit.